LASERWELDINGMALAYSIA.COM
Laser Welding Advantages
Discover the benefits of our advanced laser welding technology for precision and efficiency in your projects.
Introduction to Laser Welding
Laser welding is an advanced fusion welding process that uses a high-energy laser beam to join metals or thermoplastics. It offers precision, speed, and minimal heat input, making it ideal for industries that demand high-quality welds. Laser welding is widely used in automotive, aerospace, medical, and electronics manufacturing due to its ability to create strong, clean welds with minimal distortion.
There are several trade name of laser welding
• Laser welding
• Laser welding machine
• Industrial laser welding
• Laser welding process
• Fiber laser welding
Advantages of Laser Welding
Discover the advantages of our advanced laser welding technology for your manufacturing needs.
2. Minimal Heat Affected Zone (HAZ)
• Unlike traditional welding methods, laser welding produces minimal heat, reducing distortion and preserving material properties.
1. High Precision & Accuracy
• Laser welding provides pinpoint accuracy, making it suitable for intricate and delicate components..
3. Faster Welding Speed
• Laser welding is significantly faster than MIG and TIG welding, improving production efficiency on thin material.
4. Deep Weld Penetration
• The high energy density allows deep penetration in a single pass within the machine capacity thickness, reducing the need for multiple layers.
5. Non-Contact Process
• The laser does not physically touch the material, reducing tool wear and maintenance costs.
• Laser welding is easily integrated with CNC and robotic systems for high-volume production.
6. Automated & Robotic Integration
7. Ability to Weld Dissimilar Materials
• It can join materials with different melting points and properties, offering more flexibility in manufacturing.
• The high precision of laser welding reduces the need for grinding, polishing, or finishing work.
8. Minimal Post-Weld Processing
9. Better Aesthetic & Strength
• Produces clean, high-strength welds with minimal spatter, ideal for visible or critical applications.
10. Environmentally Friendly
• Generates less waste, consumes less energy, and eliminates the need for filler materials in many cases.
Who Should Own a Laser Welding Machine?
Laser welding is ideal for:
• Manufacturers in Automotive, Aerospace, and Medical Industries
• Job Shops & Custom Fabrication Businesses
• Sheet Metal Industries
• Electronics & Battery Manufacturers
• Jewelry Makers & Watch Repair Specialists
• Industrial Robotics & Automation Companies
• Metal Additive Manufacturing & 3D Printing Firms
• General thin material welding
• Small Businesses: With affordable handheld laser welders now available, even SMEs can adopt this tech.
How to Choose the Right Laser Welding System
1. Identify Your Welding Application
Consider the type of work you need the laser welder for: • Industrial Manufacturing (Automotive, Aerospace, Medical) → High-power fiber laser welding • Jewelry & Electronics → Precision laser spot welding • General Fabrication & Repairs → Handheld laser welding • Battery & Micro-welding → Pulsed laser welding
2. Select the Right Laser Type
Laser Type Best For Advantages Fiber Laser Industrial applications, thick metals High power, deep penetration, low maintenance Pulsed Laser Thin materials, electronics, jewelry High precision, minimal heat-affected zone Continuous Wave (CW) Laser High-speed welding, automation Fast processing, strong welds CO₂ Laser Non-metallic materials, plastics Smooth welds, good for polymers Recommendation: Fiber lasers are the most versatile and widely used for metal welding.
3. Consider Power Output & Penetration Depth
• Low Power (100W - 500W) → Best for precision applications (jewelry, medical devices). • Medium Power (500W - 2kW) → Good for general manufacturing and fabrication. • High Power (2kW - 6kW) → Required for thick metals and industrial automation.
4. Choose Between Handheld vs. Automated Systems
• Handheld Laser Welding Machines • Best for job shops, repairs, and flexible welding tasks. • Ideal for small businesses or workshops. • Automated Laser Welding Systems • Suitable for mass production and precision applications. • Integrates with CNC and robotic arms for efficiency.
5. Check Material Compatibility
Different materials require different laser settings: Material Laser Type Power Level Stainless Steel Fiber Laser Medium to High Aluminum Fiber Laser High Copper & Brass Fiber or Pulsed Laser High Plastics CO₂ Laser Low to Medium
6. Evaluate Cooling and Maintenance Requirements
• Air-cooled systems → Suitable for low-power applications. • Water-cooled systems → Required for high-power lasers (better heat management). Tip: Choose a low-maintenance fiber laser for industrial use to reduce downtime.
Choosing the right laser welding system depends on several factors, including material type, thickness, production volume, and automation requirements. Below is a step-by-step guide to help you select the best system for your needs.
7. Consider Beam Delivery and Spot Size
• Small spot size (0.1mm - 0.5mm) → High precision for micro-welding. • Larger spot size (1mm - 3mm) → Better for deep penetration and large welds.
8. Software & Control Features
• CNC & Robotic Integration → Ideal for automated production lines. • Adjustable Pulse Duration & Frequency → Provides better control over weld quality. • Real-time Monitoring & Sensors → Ensures quality control and consistency.
9. Safety & Compliance
• Ensure the system meets industry standards (ISO, CE, FDA for medical applications). • Use protective gear (laser safety glasses, enclosures). • Check for proper ventilation if working with hazardous materials.
10. Budget & ROI Considerations
Laser welding systems range from $5,000 to $500,000, depending on: • Power & Features (Handheld vs. Industrial) • Automation Level • Customization & Software Integration ROI Tip: A laser welding system pays off in high productivity, lower material waste, and reduced post-processing costs.
Final Recommendation
For Small Shops & Repairs: ✅ Handheld Fiber Laser Welder (100W - 1500W) For Medium-Scale
Manufacturing: ✅ Tabletop or Semi-Automated Fiber Laser (500W - 2kW) For High-Volume
Production: ✅ Fully Automated CNC or Robotic Laser Welding (2kW - 6kW)
How Laser Welding Improves Productivity
1. High Welding Speeds
o Laser welding uses a concentrated beam of light to melt and fuse materials rapidly. Unlike traditional methods like MIG or TIG, which require slower manual or semi-automated processes, laser welding can complete welds in a fraction of the time. For example, in automotive manufacturing, laser welding can join metal sheets at speeds up to 10 meters per minute or more, depending on the material and setup. o Impact: Faster weld times mean more parts processed per hour, directly boosting output.
2. Reduced Setup and Downtime
o The non-contact nature of laser welding eliminates the need for frequent tool changes or electrode replacements, common in MIG (wire electrodes) or TIG (tungsten electrodes). Modern fiber laser systems also require minimal maintenance compared to older CO2 lasers.
o Impact: Less downtime for adjustments or repairs keeps production lines running smoothly and consistently.
3. Automation Integration
o Laser welding systems are highly compatible with robotic arms and CNC machines. Automated setups can operate 24/7 with pre-programmed patterns, reducing reliance on skilled labor and enabling continuous production.
o Impact: Automation minimizes human error, ensures repeatability, and allows for higher throughput, especially in high-volume industries like electronics or automotive assembly.
4. Minimal Post-Processing
o Laser welding systems are highly compatible with robotic arms and CNC machines. Automated setups can operate 24/7 with pre-programmed patterns, reducing reliance on skilled labor and enabling continuous production.
o Impact: Automation minimizes human error, ensures repeatability, and allows for higher throughput, especially in high-volume industries like electronics or automotive assembly.
The laser welding service exceeded my expectations with precision and speed, truly a game changer for my projects.
John Doe
Impressive results from the laser welding! The quality and efficiency have significantly improved our production process.
Jane Smith
★★★★★
★★★★★
Contact us Now
© 2025. All rights reserved.
VINXUS MARK SDN. BHD.
Registration No. 202501007898 (1609312H)
Office:
17-1, Jalan Sentosa Villa 1/1, Taman Sentosa Villa,4300,Kajang,Selangor
Factory & Warehouse:
N-Tatt Building, No.2, Jalan Tp 5, Taman Perindustrian UEP
Subang Jaya,47600 Subang Jaya, Selagor
Lot 9124, Jalan Telok Gong, Kg Perajurit, 42000,
Pelabuhan Klang, Selangor
Lot 40, Jalan P10/16, Tmn Ind Selaman,43560,
Bandar Baru Bangi, Selangor
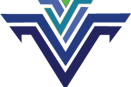

No Contact:
+6010-382 2260
sales@laserweldingmalaysia.com